Implementing continuous process optimization
How Navigance helps plant teams optimize their process around the clock with a tailored implementation of our hybrid process models, advanced data analytics tools and ongoing expert advice.
In this article we’ll look at the key stages involved in implementing the Navigance Optimization Engine.
- How we check your plant’s digital readiness
- Identifying its optimization potential
- Building a hybrid process model for your plant
- Collaborating with your plant team for successful optimization
If you’re looking for a more detailed explanation or practical examples, please request our full implementation guide.
Getting started
Are you of the same mind as the 76% of chemical producers who told us they know artificial intelligence technologies will make a big impact on operational efficiency?
If so, perhaps you’re unsure how to introduce and make the most of such technologies, or how much of your own time, money or resources you’ll need to invest in doing so.
Whatever your circumstances, you’ll want to be confident the steps you take now will be the right ones long term, before you get too far down the line. Which is why a carefully planned and expertly realized implementation is so crucial.
We have good news. While all producers’ needs differ and deployment should be tailored to suit their particular setups and goals, there are some common steps you can take to ensure successful implementation. Here, we take a top-level look at how Navigance does it.
From assessing your digital readiness and optimization potential to deploying a custom solution and activating the secure data feeds that put it to work, we aim to help you take each step smoothly by removing much of the legwork. And our support doesn’t end once you’re up and running.
Confirming digital readiness and optimization potential
Many chemical operations need to make a convincing business case to receive the funding and resources needed to introduce new technologies. For this, Navigance offers a comprehensive Benefit Assessment based on your plant’s data.
We start with a digital readiness check. This helps to identify the right use cases for digitalizing your chemical operation, key areas for improvement, and where the greatest potential to optimize exists.
As part of this assessment, we study the specifics of a plant, its process flow, logical connections, the sensors and data available along it, key variables and any constraints. Our experience and research findings show most plants are already collecting vast volumes of data from across their operations, even if they’re not yet using it to its full potential.
Typically, we ask plants to share 3-12 months of this data to determine if its quality and quantity is sufficient for us to build a hybrid process model of the plant (more on this later).
We find most plants, even those with older designs, meet the minimum requirements to start or continue their digitalization journey. And if we find any key sensors or parameters are missing, where possible we use the available data to add ‘soft sensors’ in the right places and improve the plant’s digital readiness.
Next, we use a range of methods to estimate the optimization potential in the plant’s chemical process. For these evaluations we apply descriptive statistics, adaptive filtering techniques, and data reconciliation methods based on process engineering knowledge. This will be combined with a cross-correlation and parameter variation analysis.
A comprehensive Benefit Assessment report explains our findings, key observations, and the improvement potential we estimate could be achieved by implementing a data-driven approach to support continuous process optimization.
Based on our experience, the assessment of process data commonly reveals optimization potential in the range of 1-3% for methanol or ammonia plants. Our implementation guide explores the approaches we use and example findings in more detail.
Implementation
Step 1: Building a hybrid process model
Based on your plant’s historic data and technical information about your process, we build a hybrid model to help realize the optimization potential.
With such model as its foundation, the Navigance Optimization Engine uses machine learning and advanced analytics tools to interrogate the data, spot patterns within it, scan for anomalies, identify opportunities, and recommend ways to fine tune the process.
Using hybrid models enables producers to optimize many different aspects of their process, from energy consumption to production output and cost of production – whatever matters to them most.
To that end, we work closely with the plant’s team to implement a detailed optimization strategy tailored to their key operational goals, factoring in any constraints and limitations, and agreeing control variables with which to increase process efficiency. These are the basis for the Optimization Engine’s recommendations and the custom user interface used to surface them.
With a plant-specific process model, goals, KPIs, and constraints all built into the solution design, a tailored Navigance solution is now effectively ready to deploy
We’ve designed the Navigance Optimization Engine to work regardless of the technology licenses or catalysts used. With base models ready to adapt to each plant’s particular setup and circumstances, deployment of a custom solution can be completed quickly, enabling plant teams to realize their optimization targets faster.
You can read more about the benefits of the hybrid model approach elsewhere on our blog.
Step 2: Activating secure data feeds
Our hybrid process models need powerful computing capacity to analyze plant data in real-time and generate optimization recommendations, so we host them in the cloud. In parallel to building the process models, and as pre-requisite to putting them into action, we establish a secure, continuous connection between the plant and our analytics services in the cloud.
For this, automated data transfer technologies collect the production data, upload it at pre-defined intervals. Our plant-specific data pipelines then clean it of all noise, discrepancies and outliers using adaptive filters, pattern-matching heuristics and other methods.
We are available to consult with your IT or digitalization team to evaluate the best option to enable automated data uploads that meet the highest security standards and fit into your existing set-up.
Data uploads typically take place every hour, though the intervals recommended for each plant will depend on the dynamics of its process, residence times and any particular optimization preferences. At all times the data is protected by robust, multi-layered security, in transit between plant and cloud servers, during storage, and at all points of connection. These measures keep production teams firmly in control of their information at all times.
These automated uploads pave the way for our analytics technologies to interrogate a stream of near real-time information and translate it into meaningful insights and actionable recommendations for fast, effective and ongoing process optimization.
Step 3: Continuous optimization
With the Navigance Optimization Engine deployed, the plant team is ready to make the most of it. With the platform’s recommendations and insights collated in a single online dashboard, they can adjust process control variable settings continually around the clock to keep their hitting critical KPIs even as conditions change.
What’s more, our unique combination of digital tools and ongoing support means the Navigance team continues to support through regular calls, providing expert analysis, insights, and optimization advice even after implementation is complete.
For more information on Navigance implementation, examples of how we’ve done it and the benefits it’s already brought to chemical producers, talk to us or request our implementation guide.
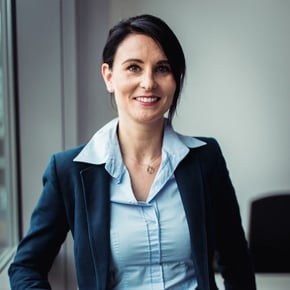