High natural gas prices drive the need to optimize ammonia and methanol production
As rising feedstock prices risk extended production freezes, Navigance offers a way to make smarter use of raw materials through chemical process digitalization and optimization.
High natural gas prices in Europe in recent months have driven many large chemical manufacturers to curb their output. In the worst cases, some have shut down production in their ammonia or methanol plants altogether.
Producers such as Achema, BASF, CF, and OCI have found the economics of operating in the current climate challenging, so have taken steps to limit capacity and reduce their negative margins.
What's driving gas price rises?
Driving the elevated prices are low stocks of natural gas in Europe and a recovery in demand in Asia. Analysts predict the trend could continue for some time, meaning producers will need to keep raw material prices under constant review and adjust their output levels accordingly.
These recent raw material and feedstock challenges are just the latest in a series of growing industry trends driving the need to optimize all aspects of chemical production processes. It’s a challenge operators must tackle at pace – and needn’t take on alone.
The importance of optimization
The Navigance Optimization Engine combines smart, cloud-based analytics technologies, hybrid chemical process models, and deep process and data science expertise in one convenient solution. Together they help optimize the most critical aspects of chemical operations on a 24/7 basis, using real-time data gathered across the plant.
The Optimization Engine is an open loop system, which provides recommendations to plant operators on how to fine tune their process to maximize its efficiency. By implementing these recommendations, the operators can stay in control of their process. The continuous optimization this makes possible has a substantial impact on plant economics and contributes to more sustainable operations.
Savings and gains through optimization
Studies by Navigance using high-resolution process data from ammonia plants have shown that continuous optimization can typically optimize the specific energy consumption per ton of ammonia produced by an estimated 1-3%. In a medium-sized ammonia plant (1000 MTPY) this translates into savings of over 5 million USD per year1. On top of that, for every 1% improvement in energy consumption per ton of produced ammonia the same plant could save more than 6,000 mt in CO2 emissions.
And there is some more good news: producers can take advantage of real-time optimization without the need for expensive upfront investment. A Navigance solution can be deployed quickly and adapted easily to suit your own specific plant setup and specifics, and targeting your most critical KPIs.
Our tailored approach enables you to focus optimization efforts where they matter most – from improving overall efficiency and output to limiting energy consumption, the cost of production and, of course, the use of raw materials.
Get in touch
If you're interested in chemical plant digitalization and advanced process controls that help you make better use of your resources, talk to Navigance today and see the difference it could make in your operation with a detailed benefit assessment.
1 Assumed natural gas price of 15 USD/ MMBtu (reference), 1% optimization and 1000 MTPY capacity.
Explore further:
Implementing continuous process optimization
How Navigance helps plant teams optimize their process around the clock with a tailored implementation of our hybrid process models, advanced data analytics tools and ongoing expert advice.
In this article we’ll look at the key stages involved in implementing the Navigance Optimization Engine.
Chemical process models – from first principle to hybrid models
In this article, we explore the role, common uses and limitations of the first principle approach to chemical process modeling. And we contrast this with the advantages and disadvantages of using empirical or statistical models.
We then look at how taking the first steps into new, intelligent 'hybrid' models can deliver the best of both approaches and more than the sum of their parts.
Why you need to optimize your chemical process now
In chemical manufacturing, the need to find ways to optimize is growing like never before. While it might still seem like a nice-to-have today, emerging and accelerating trends in the industry and other external factors will mean it’s increasingly a necessity.
Read More
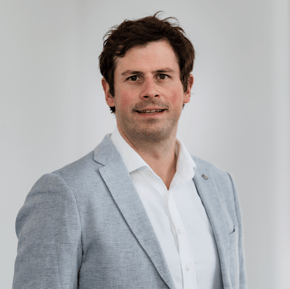