Digitalization: a roadmap for chemical plants
We would like to continue sharing highlights from extensive Navigance research conducted with people in various roles across the chemical manufacturing sector. Now we focus on the journey of digitalization in chemical plants.
In our last article, we summarized the realities of their day-to-day operation, their most pressing needs, and how digitalization is already adding value for them – or could do in the future. We also highlighted how our insight suggests three common steps to digitalization can be followed whatever your level of digital maturity and most pressing needs are now.
What’s in this article?So, in this second part of the story, we’ll look at those steps in more detail.
- Step 1: Data visualization and sharing
- Step 2: Increasing plant availability
- Step 3: Optimizing process efficiency
Three steps to fully realize the potential of digitalization in your plant
A common roadmap
Despite all of the differences we’ve seen across the chemical manufacturing sector, Navigance found it’s possible to follow some common steps to digitalize your operation the right way and at the right pace.
We believe you can adopt this roadmap for success now, whatever your starting point is. And it includes options that won’t place a huge demand on your own in-house resources, including world-class third-party support.
In fact, a single partner can provide digital technology to make each step easier when the time’s right to take it, complementing the technology investments you’ve already made and the self-service tools you already get value from using.
Our own digital tools easily augment these and each other, for a smooth transition from step to step. And they’re backed by deep process and data science expertise plus ongoing support to make the most of them. For a digital journey that’s bump-free.
So, let’s look at each step on that journey in turn.
Step 1: Data visualization and sharing
For chemical producers in the earliest stages of digitalization, the first step is to take the data being gathered across their plants and see, interpret, and use it more effectively. The key technology need at this stage is data visualization and sharing.
In most plants, their DCS, data historian(s) and any self-service tools – commonly deployed on-premise – help to provide a first clear and comprehensive real-time picture of the plant environment and its processes.
Armed with this single view of reality, plant teams can conduct more advanced analysis of any patterns they see in their real-time and historical data, share secure, rights-based access with the right people, and collaborate more effectively in the right areas.
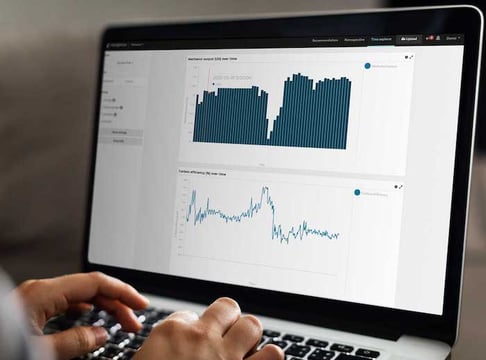
As a cloud-based solution, the Navigance Performance Manager, for example, introduces an extra dimension. It allows teams to share data across different locations, keeping plant personnel continuously informed and, where needed, partners too. It’s an easy and effective way to tap into the right in house or outside expertise. And it’s all done via a web-based service, whereas before it would typically have been email-based.
Data visualization and sharing like this creates the foundation for doing more with your data. As such, it’s the basis for all Navigance services, coming as standard with both the Navigance Plant Monitor and Navigance Optimization Engine. But it’s also only the start.
And if you already have implemented another data platform, we can just plug-in to it and make the Navigance services available even faster.
Step 2: Increasing plant availability
As we heard in our previous article, the predominant need for those still in the early stages of digitalization is to either increase or consistently maintain plant availability. And, once a clearer view of plant and process data is in place, it’s easier to take the next step in order to achieve it.
Due to the strong impact on the operational goals output and cost:
For plant availability it is "the more, the better",
at the cost of higher invest and maintenance.
Often used interchangeably with plant “reliability”, availability is usually measured by Operational Equipment Effectiveness (OEE)or plant uptime. And it strongly influences the common priorities in chemical operations of meeting agreed output levels, and doing so within budgeted costs.
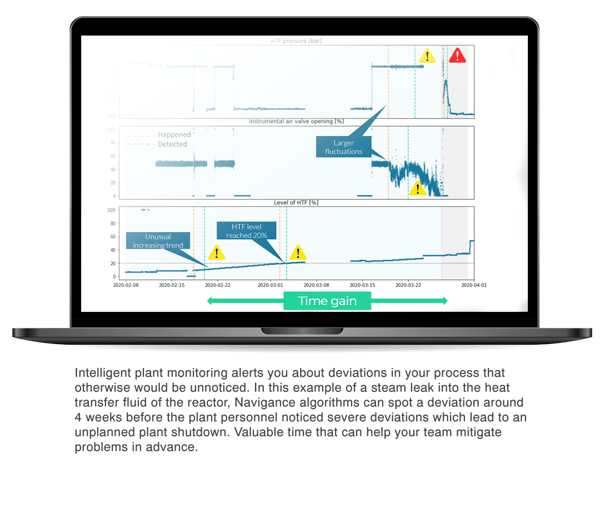
Since any downtime reduces the capacity for production while increasing its costs, the common feeling among our interviewees was “the more availability we have the better.” Most of those we spoke to recognized achieving that came at the cost of higher investment in equipment and maintenance.
The opportunity digital tools present is to help focus that investment and maintenance more precisely and effectively, anticipating, and intercepting issues early, speeding up remedies, and reducing costs.
“If proactive alerting prevents just one period of downtime, then it quickly pays for itself.”
Senior Process Engineer, Ammonia plant
While some digital solutions have proved useful for retrospective analysis and remedial action, the Navigance Plant Monitor enables plants teams to take a much more proactive approach. Built on real-world expertise in chemical processes, it automatically monitors process variables around the clock and provides 24/7 alerting of any issues or deviations it observes in the data.
These alerts are more advanced alerts than those typically provided by a plant’s DCS system with fixed limits – warning, for instance, of faster rate-changes of variables, deviations from typical patterns, and similar unusual behavior. Receiving these notifications before any process limit is hit enables customer operations teams to review the data and take appropriate, focused action quickly, before issues ever become problems.
“If proactive alerting prevents just one period of downtime,” one interviewee told us, “then it quickly pays for itself.” Another pointed out the potential for advanced alerting to overcome downtime due to people-related issues – such as having insufficient time or tools to bring the finest details of any aspects of the operations into focus at any given moment.
Step 3: Optimizing process efficiency
Once a consistent, high level of availability has been achieved, the next step on the digitalization journey is to use your data to fine-tune your chemical process.
Like availability, process efficiency – whether measured in yield, energy use, selectivity, feedstock cost, emissions or by some other means – affects a plant’s ability to deliver its agreed output levels and do so within budget.
So when is the right time to increase your focus on optimizing it? Over 80% of the industry experts Navigance asked saw a consistent OEE of 90% or above as the point at which they’d consider the shift. And over three quarters saw artificial intelligence as a technology with real potential to add value when they do.
The sheer scale and complexity of their operations means they or their teams lack the time for anything more than basic data analysis to inform efficiency improvements. Even then, it can be difficult to know if any action they do take will result in a marked improvement.
Introducing digital technologies such as machine learning can take the burden of spotting opportunities to improve efficiency off plant team’s shoulders, leaving them free instead to act as they see fit on the technology’s recommendations.
The Navigance Optimization Engine, for example, uses highly adaptive hybrid plant models built on our extensive process domain knowledge and enhanced with machine learning.
This combination analyzes real-time and historic plant data and gives recommendations on how to fine tune process control variables. The result: plant personnel can take actions confidently to continuously optimize their process towards achieving their particular goals.
Within the same Navigance Data Platform interface, teams working on site or remotely can review patterns in the data and any improvement recommendations together, and make fast, informed, effective decisions. Tuning the finest details of their process control variables to continuously optimize.
A growing urgency for efficiency
Right now, process efficiency is sometimes seen as a “nice to have,” one that’s readily sacrificed if needed to secure plant availability. But its importance, and the need to focus attention on it, will only grow as conditions in the chemical industry continue to evolve.
“If we don’t need to fully utilize the plant any more, our focus will turn towards efficiency.”
Production manager based in the US
Consider the likelihood of economic downturn and the need to do more with less, as resources get stretched and ways of working change. Recognizing the implications, one interviewee told us: “If we don’t need to fully utilize the plant any more, our focus will turn towards efficiency.”
The coming years will also be marked by an increased focus on sustainability beyond simply offsetting carbon footprints. How you use raw materials, and how much raw material you use, will come under increased scrutiny. What better way to address this need than smart ways to optimize the finest details of your process?
Another challenge is how to replace gradually lost experience to retain current performance levels or, better still, push beyond them. Improving process efficiency, and specifically doing so with smart digital tools, can provide access to a mine of data, patterns and knowledge that helps filling competency gaps and enables the next generation to flourish.
The producers that respond best to these trends are likely to be those that start planning for them early.
Take your next step with Navigance
Navigance can be your partner with a solution for every step of the digitalization journey – from shedding new light on your plant data to maximizing uptime and optimizing your process.
We know the challenges operators in the industry face and bring a unique combination of technology, products, and ongoing service to support you and take the pressure of your own teams but keep you in the driving seat of your transformation at all times.
With our roots in Clariant, one of the world’s leading chemical producers, we bring not only data science and analytics expertise but also long-standing, real-world chemical domain experience to the table. And a methodology that’s been sense checked with professionals working in the industry’s many fields in companies all around the world.
In future blogs, we’ll be looking in more detail at every phase of the digitalization journey and how digital technologies can add value for you at each stage. In the meantime, you explore further with the articles and white paper below.
Or contact Navigance if you’re ready to take your next step.
Explore further:
Optimizing chemical production using data-driven, AI-enabled hybrid modeling
Smart use of your plant’s data can take process efficiency to a higher level. Hybrid models driven by artificial intelligence deliver the best results for the least effort. And you don’t need a data science degree to enjoy them.
Read More
Navigance white paper:
Make technology work for you, not more work for yourself.
AI-enabled data analysis unlocks hidden process optimization potential, effortlessly and without tying up your resources. Our free white paper reveals where to start.
Read More
Read the Nitrogen+Syngas article on our fresh approach.
Discover the growing importance of technical services for chemical producers.t.
Download the article
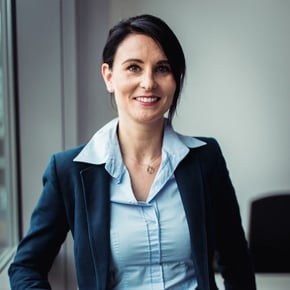