Why you need to optimize your chemical process now - part 1
In chemical manufacturing, the need to find ways to optimize is growing like never before. While it might still seem like a nice-to-have today, emerging and accelerating trends in the industry and other external factors will mean it’s increasingly a necessity.
Here, we focus on some of the most pressing issues, the challenges they present for chemical producers, and how the path to addressing and overcoming them may not be as complex or resource intensive as some may fear.
What’s in this article?
In this first half of a two-part article, we’ll look at the conflict between producers’ apparent readiness to optimize their chemical process versus the first of three sector trends driving the urgency to do so:
- Economic downturn – including the impact of Covid-19
Then in the second half, we’ll consider two other critical drivers for change:
- An ageing workforce – and a looming experience crisis
- A growing emphasis on sustainability
Throughout, we’ll hear how digitalizing with the right combination of technology and expert support can help to tackle these challenges sooner rather than later.
If you aren’t already optimizing, it’s time to start.
Accelerating industry trends mean it’s more important than ever.
When Navigance asked close to 40 chemical manufacturing experts working in different roles within the sector when they would be prepared to optimize their chemical process if they hadn’t already done so, the answer was fairly unanimous.
They told us their top priority was maintaining high levels of safety in their operations. That was followed by a focus on maintaining the availability of their plant and process, to reduce the potential for and negative impacts of downtime.
Only once they were consistently achieving high levels of operational safety and uptime, producers said, would they realistically turn their focus to fine-tuning aspects of their process. That’s despite most recognizing digital technologies have a key role to play in helping them do so – and already do for the most advanced players.
As we’ve explored in our free process optimization white paper, one of the biggest barriers to optimization and digitalizing in general is the time and expertise needed to do it properly. Resources that often can’t be spared from the day-to-day running of operations.
Nevertheless, the industry is already feeling the effects of certain trends and other factors that, increasingly, will make optimizing not just desirable but also essential. Especially as their impact on producers accelerates in the coming years.
For one thing, there’s the ongoing effect of economic downturn on the sector, particularly with the added pressures caused by the Covid-19 pandemic. There’s also the loss of long-standing and often invaluable experience as large proportions of the workforce get older and retire.
What’s more, an increased focus on the sustainability of operations in the coming years will demand new ways to make optimum use of resources and tangibly reduce the impact of operations, rather than merely offset it. None of these trends should be ignored.
Economic downturn
Look back over the last 10-13 years in the chemical industry and you’ll find a story of ups and downs.
A downturn after the 2008 financial crisis was followed by a sustained period of growth in areas such as petrochemicals from 2010 to 2018. Then things slowed again in 2019 as the sector faced declining demand but overcapacity, growing pricing pressure and uncertain trading1.
Then, of course, Covid-19 struck. Besides causing supply chain disruptions, falling prices and a severe drop in demand in many end markets, one of the starkest indicators of the pandemic’s impact on chemical production has been its effect on jobs.
In the 12 months from September 2019, more than 32,000 production jobs were lost across the chemical industry2. And while some plants were able to mobilise quickly to adapt their operational structures and ways of working, others were less fortunate and shut down entirely.
Although a recovery of sorts is forecast during 2021, it will take some time to return to 2019 levels, and longer still to achieve the kind of impressive growth seen earlier still. In the near term, at least, perhaps the only real certainty is more uncertainty. So it’s important to be ready for it.
Working smarter
Doing the most you can with what you have – the very essence of optimization – will take on even greater importance in the months and years to come.
Having fewer production staff will mean putting those who remain to the best possible use. That might seem to be the day-to-day running of the plant. But, in fact, freeing them up from these repetitive tasks could enable more effective use of this valuable and now scarcer resource elsewhere.
Meanwhile, continued overcapacity in the sector will mean low utilization levels and the need to make sure that, when plants are running, not a scrap of their potential is wasted. That’s tricky to achieve with fewer people.
Digital technologies can help on both counts. During the coronavirus crisis, they proved invaluable for all kinds of industries, helping those who could work from home stay productive and connected to those still braving the front line.
In chemicals, the benefits for the most digitally mature operators went further still. Those already using technologies such as machine learning to help monitor and optimize their operations were often at an advantage over their rivals, able to collaborate on fixes, improvements and more efficient ways of working.
With tools such as the Navigance Plant Monitor and Navigance Optimization Engine, for instance, plant teams can focus their time and attention where it matters most. From proactively identifying issues or anomalies for an early, targeted response, to identifying ways to optimize automatically, so personnel can act on them with confidence.
According to Deloitte, demand for such digitalization of core processes will only intensify as a result of the Covid-19 experience. Will you be among those putting them to work?
Accelerating trends in the chemical and materials sector (Source: Deloitte analysis)
Continue reading in part 2 of this article:
In the second half of our look at the trends driving the need to optimize, we’ll explore how digital tools can help you overcome the skills gap as an experienced but ageing workforce retires. The opportunity is to optimize more effectively then ever before.
And how your plant could make more efficient use of resources and raw materials, to operate more sustainably sooner rather than later, through digital optimization.
Click here to continue with part 2 of this article.
1 The impact of COVID-19 on the global petrochemical industry (McKinsey, October 2020)
2 2021 Chemical Industry Outlook (Deloitte, 2020)
Explore further:
Optimizing chemical production using data-driven, AI-enabled hybrid modeling
Smart use of your plant’s data can take process efficiency to a higher level. Hybrid models driven by artificial intelligence deliver the best results for the least effort. And you don’t need a data science degree to enjoy them.
Read More
Navigance white paper:
Make technology work for you, not more work for yourself.
AI-enabled data analysis unlocks hidden process optimization potential, effortlessly and without tying up your resources. Our free white paper reveals where to start.
Read More
Opportunities for data-driven analytics: Nitrogen+Syngas magazine feature
Read in the March/April 2021 edition how you could benefit from data-driven analytics
Download the article
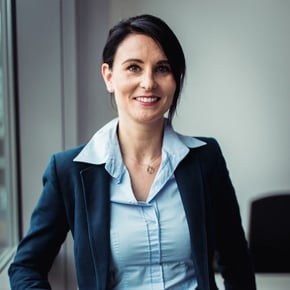